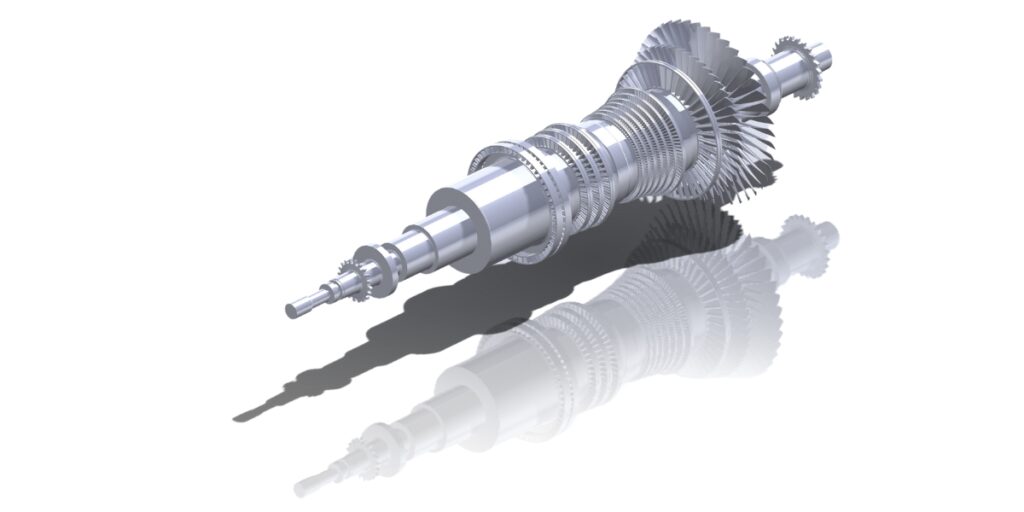
Steam Turbine Re-rates and Redesign
Whether for increased efficiency, improved reliability, increased/decreased power, or changed operating conditions, the steam turbine re-rate involves the following steps:
- Acquisition of existing steam path geometry
- Development of a computer model for performance simulation
- Performance simulation and evaluation of results
- Steam path redesign
- Mechanical analysis and design iteration
- Steam path modification
Steps 3, 4, and 5 must usually be repeated numerous times as design inputs such as rotordynamics, structural strength, thermodynamics, manufacturing cost, and delivery time may conflict.
The Illustrated Steps
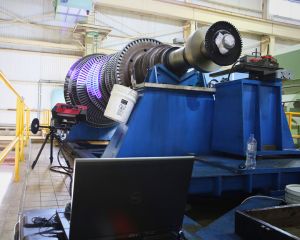
STEP 1: GEOMETRY ACQUISITION
The first step in the steam turbine re-rate process is to obtain steam path geometry, which can be done manually with precision and semi-precision measurement tools for relatively small turbines, or digitally (laser or structured light scanning), for larger turbines that feature radially varying blade sections.
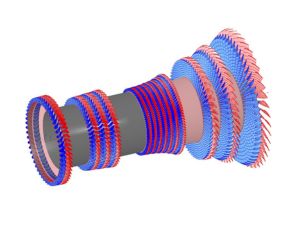
STEP 2: COMPUTER MODEL DEVELOPMENT
After acquiring the original geometry, the next step in the steam turbine re-rate process is to develop a computer model. Macek Power uses both proprietary in-house and commercially developed software for modeling, depending on turbine type. The computer model represents both steam path geometry and boundary conditions such as shaft speed, extraction flows, and thermodynamic properties of the steam at inlet and exhaust.
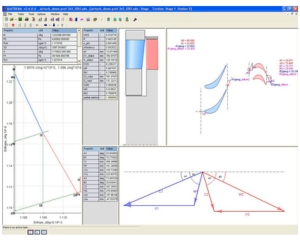
STEP 3: SIMULATE PERFORMANCE
The third steam turbine re-rate step is where the computer model is used to numerically simulate thermodynamic performance. Model geometry and operating conditions can be changed to examine their effects and/or to thermodynamically optimize a design.
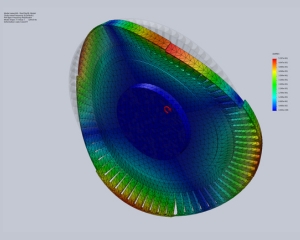
STEPS 4 & 5: REDESIGN, MECHANICALLY ANALYZE, AND ITERATE
After it is reasonably believed that the design has been thermodynamically determined, the next steps are to validate the design for structural integrity, dynamic stability, and economic feasibility. Other design inputs, such as the results of finite element and rotordynamic analysis studies, are considered as needed to ensure a reliable design. These additional mechanical analyses often require a return to Step 3. This loop repeats until a satisfactory design is produced.
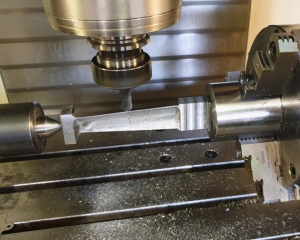
STEPS 6: STEAM PATH MODIFICATION
With the design work complete, the final step in the re-rate process is steam path modification. This may include reducing the number of stages in the steam path, changing the stationary flow area of already existing nozzles and diaphragms, or manufacturing replacement steam path components.
Macek Power typically completes several steam turbine re-rates per year. Engineering experience with the re-rate process dates back to 1995, well before Macek Power was established.